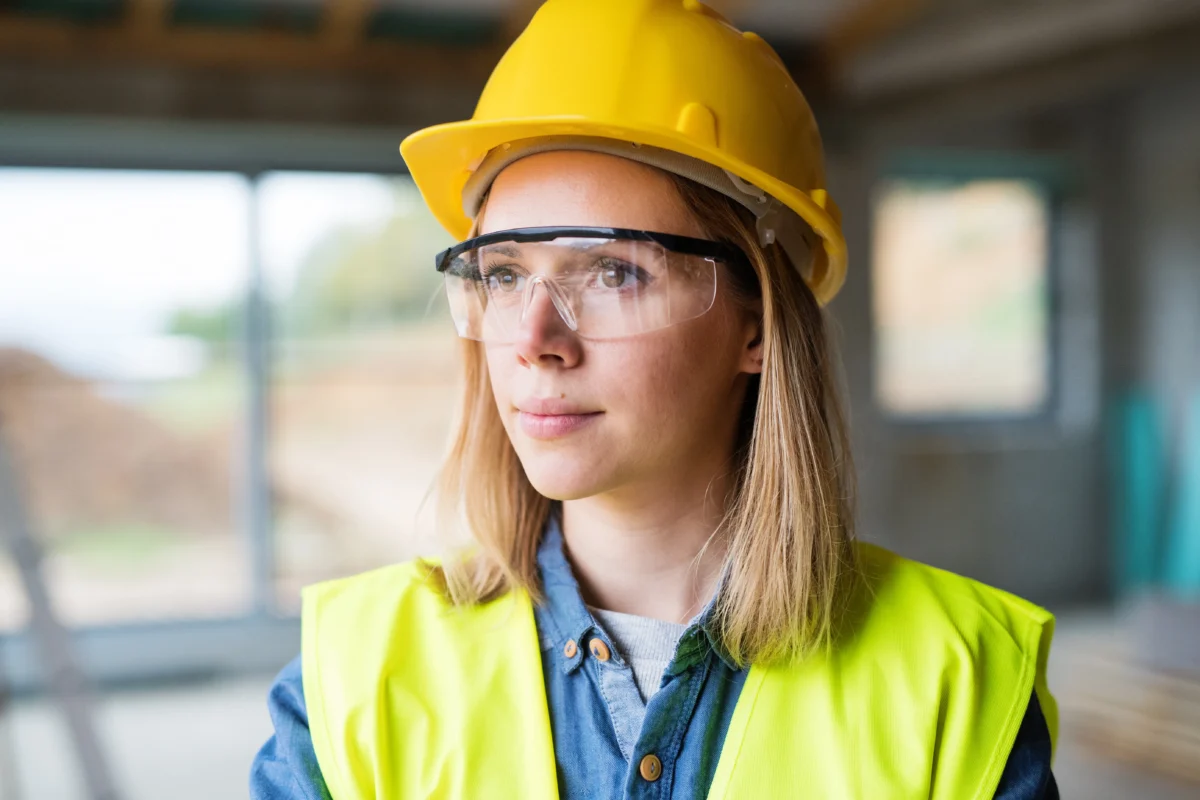
As building initiatives develop in complexity and scale, the necessity for environment friendly and efficient upkeep methods will increase exponentially. Even small delays attributable to building gear downtime can throw a mission off schedule, rising a variety of prices. With a complete preventive upkeep (PM) program backed by a contemporary software program answer, building professionals can scale back the dangers related to breakdowns.
Why is gear downtime so expensive in building?
Downtime gear in building is expensive due to a number of interconnected elements.
Idle gear results in delayed mission timelines, which can lead to vital monetary penalties and lack of popularity. Every day a mission falls delayed can translate into additional prices for added labor, materials, and potential contractual fines.
The direct prices of repairing or changing malfunctioning gear can be substantial. Surprising breakdowns usually require emergency repairs, that are usually costlier than routine upkeep. Moreover, the price of renting substitute gear to maintain the mission on monitor can additional add to bills.
Gear downtime disrupts the fastidiously deliberate workflow, resulting in inefficiencies and lowered productiveness. Keep in mind, mission administration for building typically follows the normal waterfall mannequin. Employees could also be left idle, ready for gear to be repaired, which wastes beneficial labor hours. This ripple impact can affect subsequent duties, inflicting a domino impact of delays all through the mission.
And frequent downtime can negatively have an effect on the lifespan of kit, necessitating earlier replacements and rising long-term capital expenditures. Common preventive upkeep is essential to mitigate these prices by figuring out and addressing potential points earlier than they trigger vital downtime. Minimizing gear downtime isn’t nearly saving cash. It’s about guaranteeing the general success and profitability of building initiatives.
How can building corporations calculate the true value of kit downtime?
To calculate the price of unscheduled downtime for gear on a building website, think about misplaced productiveness, restore prices, and extra bills similar to rental gear or additional time labor.
Misplaced productiveness: Calculate the hourly output of the gear and multiply by the hours of downtime.
Restore prices: Embody elements, labor, and any diagnostic charges.
Extra bills: Embody rental gear to exchange the downed machine plus any additional time labor if staff must catch up.
For instance, a bulldozer strikes 200 cubic yards of grime per hour. If it’s down for eight hours, that’s 1,600 cubic yards not moved. Repairing the bulldozer prices $5,000 in elements and $3,000 in labor. And renting a substitute bulldozer prices $2,000 per day, and additional time labor is $1,500.
Misplaced productiveness: 1,600 cubic yards at $2 per cubic yard = $3,200
Restore prices: $8,000
Extra bills: $3,500
Complete value of unscheduled downtime: $3,200 + $8,000 + $3,500 = $14,700
This instance is probably going a best-case state of affairs for building gear downtime as a result of it doesn’t embody the price of the work delays between the primary bulldozer breaking down and the substitute arriving. As soon as the work is off schedule, each different aspect of the mission wants recalibration to fulfill an adjusted timeline. So, the rebar may now go in late, and the cement vehicles may must be rescheduled, too.
How can building corporations forestall unplanned downtime with preventive upkeep?
A PM program performs an necessary function in preserving building gear on-line, guaranteeing longevity, reliability, and cost-effectiveness. Common inspections permit for early detection of points, stopping minor issues from escalating into main failures that trigger vital downtime. For instance, checking a crane’s hydraulic system can establish leaks or worn hoses, that are cheap to repair however might result in catastrophic failures.
Scheduled upkeep duties, similar to oil adjustments, filter replacements, and lubrication, preserve gear operating easily and prolong their lifespan. These duties forestall extreme put on and tear, decreasing the necessity for untimely part replacements. For instance, commonly altering the engine oil on an excavator can delay engine life, saving 1000’s of {dollars} in potential restore or substitute prices.
A PM program also can enhance security on building websites. Effectively-maintained gear is much less more likely to malfunction, decreasing the chance of accidents and accidents. Inspections additionally be sure that security options, like backup alarms and emergency stops, are functioning accurately.
And well-documented upkeep data can improve resale worth, offering a complete historical past of the gear’s situation and maintenance. In abstract, preventive upkeep not solely saves money and time but additionally promotes security and preserves the worth of building gear.
How does preventive upkeep software program assist building corporations forestall downtime?
PM software program helps with streamlining processes and enhancing effectivity. Backed by the suitable answer, upkeep groups can:
- Eradicate difficult upkeep workflows: Automates scheduling, assigns duties, and tracks progress, decreasing guide effort and minimizing errors
- Retain beneficial data from senior techs: Captures institutional data by documenting upkeep procedures and historic information, guaranteeing experience is saved and shared
- Allocate sources seamlessly: Gives real-time visibility into gear standing and technician availability, enabling dynamic useful resource allocation and improved productiveness
- Maintain your complete crew related from anyplace: Presents cell entry, permitting area technicians to replace work orders, entry documentation, and talk with the crew remotely
- Unify your information right into a single related database: Centralizes gear historical past, upkeep data, and stock information, enabling knowledgeable decision-making and simplifying audits
By addressing these elements, preventive upkeep software program helps the upkeep crew enhance gear reliability, scale back downtime, and improve operational effectivity.
What are the steps for implementing a PM program in building?
Implementing a PM program requires a scientific strategy that includes steady enchancment.
Assess present upkeep practices
Earlier than implementing a preventive upkeep program, it’s necessary to grasp your present upkeep practices. Conduct a radical audit of your current processes, gear historical past, and failure patterns. Determine which belongings are most crucial to your operations and that are most liable to breakdowns. Additionally consider your present upkeep methods, together with reactive and preventive measures, to find out what’s working and what’s not. An intensive evaluation helps you pinpoint areas that want enchancment and set a baseline for measuring the success of your new program. Moreover, contain your upkeep crew on this course of to collect their insights and acquire buy-in.
Implement a digital PM platform
A digital PM platform is the spine of a contemporary, environment friendly upkeep program. Spend money on a complete software program answer that helps you meet the precise wants of the development trade. Key options to search for embody:
- Gear monitoring
- Automated work order technology
- Upkeep scheduling
- Stock administration
- Actual-time analytics
The platform also needs to supply cell entry, permitting technicians to replace work orders and entry documentation from the sphere. To make sure a clean implementation, appoint a devoted mission supervisor, contain your data expertise division, and have a look at following a phased rollout. Be sure there’s sufficient coaching so all customers are comfy with the brand new system.
Develop a upkeep schedule
Along with your digital platform in place, the following step is to develop a upkeep schedule in your gear. Begin by gathering producer suggestions for every asset, together with inspection intervals, lubrication necessities, and part substitute schedules. Then, modify these suggestions based mostly in your gear’s precise utilization and working situations.
For instance, gear uncovered to harsh environments could require extra frequent upkeep. Enter this schedule into your digital platform, which ought to mechanically generate work orders based mostly on meter readings or calendar intervals. Recurrently evaluate and replace your upkeep schedules to make sure they continue to be related and efficient.
Practice the crew
The success of your program hinges on the help and competence of your crew. Present complete coaching on the brand new program, together with the digital platform, upkeep schedules, and procedures. Guarantee all stakeholders perceive their roles and tasks, from technicians performing the upkeep duties to operators reporting gear points, and administration overseeing this system. It’s necessary to foster a tradition of proactive upkeep, encouraging everybody to take possession of kit well being. Recurrently refresh this coaching to maintain this system prime of thoughts and replace your crew on any adjustments to the processes or software program.
Monitor, analyze, and optimize
Steady monitoring and evaluation are important to maximise this system’s advantages. Use your digital platform to trace key efficiency indicators (KPIs) similar to gear downtime, imply time between failures (MTBF), and upkeep prices. Recurrently evaluate these metrics to establish traits, pinpoint drawback areas, and measure this system’s effectiveness. Use this information to refine your upkeep methods, optimize schedules, and enhance procedures.
Encourage a cycle of steady enchancment, all the time on the lookout for methods to enhance gear reliability and scale back upkeep prices. Recurrently talk this system’s successes and classes discovered to your crew to take care of engagement and momentum.
It’s necessary to do not forget that with any upkeep program, implementing the suitable expertise is just ever a part of the answer. In an episode of the Asset Champion podcast, visitor Cameron Christensen, CEFP, FMP, and Director of Asset Administration for Services Operations at Princeton College, explains how expertise is one piece of the puzzle.
“Know-how will not be the technique. It’s an accelerator of technique. It’s an important piece of our technique, nevertheless it’s not the technique itself.”
How does a digital preventive upkeep platform assist minimize building gear downtime?
Implementing a contemporary PM platform helps streamline building upkeep operations. By automating scheduling, assigning duties, and monitoring progress, the platform helps remove difficult workflows, reduces guide effort, and minimizes errors. It helps the upkeep crew seize and protect institutional data from skilled technicians by documenting upkeep procedures and historic information, guaranteeing experience is shared. And since it gives cell entry for area technicians to replace work orders, entry documentation, and talk remotely, the complete crew stays related, boosting time on wrench and general productiveness.