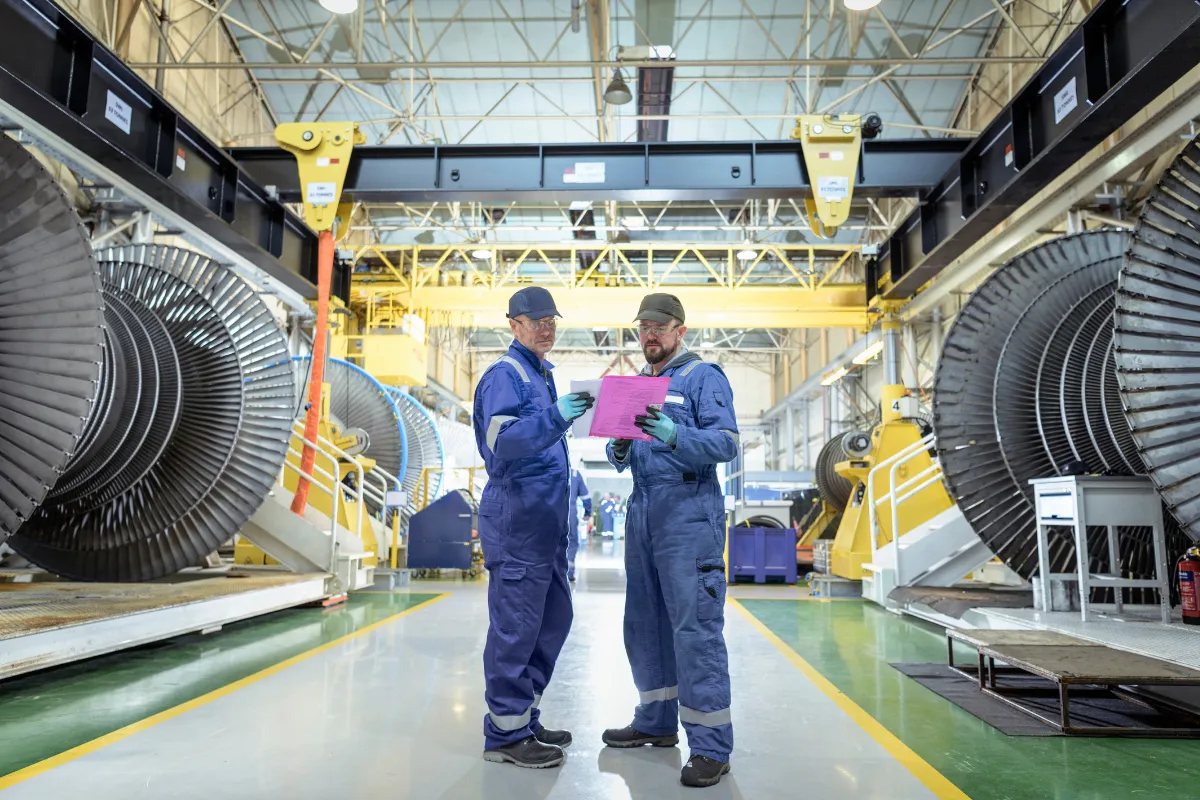
In large-scale operations like manufacturing, healthcare, and amenities administration, effectivity is the inspiration of success. When upkeep workflows are well-organized, groups can reply swiftly to repairs, hold tools operating easily, and stop pointless prices.Â
For upkeep groups dealing with a whole lot and even hundreds of property, a structured work order system ensures seamless coordination—technicians know precisely what wants consideration, managers have clear visibility into progress, and upkeep duties are prioritized successfully.Â
By adopting a centralized and automatic strategy to work order administration, organizations can eradicate inefficiencies, streamline operations, and hold all the pieces operating at peak efficiency. Â
That is the place a Computerized Upkeep Administration System (CMMS) turns into a game-changer. By automating work order administration, a CMMS eliminates guesswork, streamlines communication, and ensures that upkeep groups concentrate on the duties that matter most.Â
Why conventional work order administration falls quickÂ
Earlier than fashionable upkeep software program, work orders have been typically managed by means of spreadsheets, paper logs, or a mixture of disconnected programs. Whereas this strategy could have labored when organizations have been smaller and property have been fewer, it rapidly falls aside as companies scale.Â
A technician would possibly obtain a printed work order within the morning, solely to search out that the tools difficulty has already been fastened — or worse, {that a} extra pressing restore has come up, however they have been by no means knowledgeable. Managers, alternatively, spend hours manually monitoring work progress, fielding calls, and making an attempt to piece collectively upkeep data from scattered stories.Â
This lack of real-time visibility results in miscommunication, delays, and missed alternatives to optimize upkeep schedules. Preventive upkeep duties is perhaps skipped or duplicated, components may not be out there when wanted, and technicians find yourself responding reactively as a substitute of proactively addressing points earlier than they escalate.Â
For organizations working a number of amenities or managing advanced equipment, these inefficiencies aren’t simply irritating — they’re expensive.Â
The CMMS benefit: Bringing order to upkeep Â
A Computerized Upkeep Administration System (CMMS) centralizes work order administration, changing fragmented processes with a streamlined, automated workflow. As a substitute of chasing down paper work orders or manually updating spreadsheets, upkeep groups can generate, monitor, and full work orders digitally — all in actual time. Â
One of the vital rapid advantages of a CMMS is automated work order task. When a problem arises, the system routinely assigns the duty to the suitable technician based mostly on availability, talent set, and placement. This eliminates the back-and-forth of manually delegating duties and ensures that work orders are addressed promptly.Â
In industries the place uptime is essential — resembling manufacturing, healthcare, and logistics — this type of automation is invaluable. As a substitute of ready for an asset to interrupt down, groups can use preventive and predictive upkeep triggers to schedule repairs earlier than failures happen. Gear downtime is minimized, and upkeep groups can work proactively as a substitute of reacting to emergencies.Â
Past work order monitoring, a CMMS additionally improves stock administration. When a technician is assigned a job, the system cross-references spare half availability, stopping conditions the place repairs are delayed attributable to lacking parts. By sustaining correct inventory ranges, amenities managers can scale back wasteful overstocking whereas guaranteeing that important components are all the time readily available when wanted.Â
Bettering accountability and compliance with CMMSÂ
For companies in regulated industries, upkeep documentation isn’t nearly effectivity — it’s about compliance. Amenities must hold detailed data of upkeep actions to satisfy business requirements, whether or not for security laws, tools warranties, or authorities audits.Â
A CMMS offers a transparent, time-stamped digital document of each work order, together with who carried out the duty, when it was accomplished, and what components have been used. This degree of monitoring reduces legal responsibility dangers, ensures regulatory compliance, and makes audits considerably simpler.Â
Technicians now not must manually log accomplished duties, and managers now not must sift by means of piles of paperwork to show that upkeep was carried out appropriately. In high-stakes environments like hospitals, manufacturing crops, and vitality amenities, this transparency is essential.Â
The way forward for work order administration: Information-driven and predictiveÂ
As expertise continues to evolve, the function of CMMS in work order administration will solely develop extra refined. The combination of IoT sensors, AI-driven analytics, and mobile-first options is making upkeep smarter, quicker, and extra predictive than ever earlier than.Â
IoT-enabled CMMS platforms can now detect anomalies in tools efficiency — resembling uncommon vibrations or temperature fluctuations — and routinely generate work orders earlier than failures happen. Which means as a substitute of reacting to breakdowns, organizations can stop them from occurring altogether.Â
Cell accessibility is one other game-changer. With CMMS cellular apps, technicians can obtain work orders, entry asset histories, replace job statuses, and even add pictures or notes — all from their smartphones or tablets. This ensures that upkeep groups keep related, even in distant or large-scale amenities.Â
The way forward for work order administration is now not about simply maintaining with repairs — it’s about making a seamless, self-optimizing upkeep ecosystem that retains companies operating easily.Â
Why CMMS is now not optionally availableÂ
Right this moment’s world strikes rapidly and is data-driven, so handbook work order administration is now not a viable choice for enterprises that need to keep aggressive. The inefficiencies of outdated programs result in rising prices, wasted time, and operational dangers that no group can afford.Â
A CMMS-backed work order administration system adjustments the sport by automating workflows, bettering response occasions, and guaranteeing that upkeep efforts are data-driven and strategic.Â
Whether or not managing a single facility or a worldwide portfolio of property, the impression is simple: much less downtime, lowered prices, and an operation that runs like a well-oiled machine.Â
The query isn’t whether or not organizations ought to spend money on a CMMS — it’s how rapidly they’ll implement one to begin seeing the advantages.Â